Performance of rail car lining materials varies wildly depending on the commodity.
Some commodities are benign enough that a general-purpose epoxy lining might last a generation. But for molten sulfur, owners and shippers are thrilled if even a high-performance epoxy or novolac vinyl ester lasts three years.
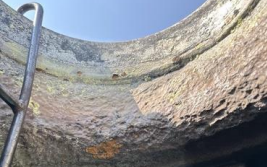
The service is just that corrosive.
And even after that short period, the standard procedure for relining a tank car in molten sulfur service is more time- and labor-intensive than for less severe commodities.
That’s because blending the substrate is commonly recommended as an extra step in surface preparation. That process and its rationale are described below.
What is substrate surface blending?
Blending is a hand-tool process in which an operator grinds away sharp edges from a surface that will be coated. It occurs prior to standard SSPC SP-3 surface preparation for tank car interiors.
The process is critical to the performance of linings of tank cars in molten sulfur service because the corrosion associated with that commodity causes significant surface irregularities in the form of deep pitting corrosion. That irregularity interferes with the uniformity in dry film thickness of an applied lining, potentially leading to its premature failure.
The objective of blending is not necessarily to eliminate the pitting commonly observed on a tank car interior surface. Instead, it is meant to alter the surface geometry just enough so that corrosion pits are within the acceptable shell thickness tolerance, and are wide and deep enough to accommodate the coating. In other words, surface flaws may remain, but they’re gentler than before.
But blending is not always appropriate. If steel is so badly corroded that it loses more thickness than regulations allow, the affected area must be removed and a patch of new steel welded in.
You can see why regular inspections of tank cars in molten sulfur service are important. It can cost $30,000 or more to completely recondition a tank car. Though blending adds even more to that total, it’s still more cost-effective than patching.
Why is substrate surface blending necessary?
Properties of sulfur and the realities of rail transportation create the conditions that make surface blending necessary.
Sulfur is almost never shipped in its solid state because it clings very well to itself and other surfaces. It’s very hard to break apart and would easily clog a hopper car. It’s far easier and faster to load and unload at a temperature above its melting point of 235°F (113°C). In addition, dry shipment would expose a rail car lining to significant abrasion and impact during loading, unloading, and while underway. The commodity is simply less physically abusive in its molten state.
The problem is, it doesn’t always stay molten. During routine loading, unloading, and transit, bits of it sometimes freeze. Tank cars are never filled completely and always have head space containing air and moisture. So if sulfur freezes, it reacts with that air and moisture to form sulfides. Dry sulfides in the presence of moisture are extremely corrosive, and deep pitting is a common outcome. It is mostly observed around the load line, manway, and bottom nozzle, where small amounts of the commodity remain after loading/unloading and inevitably freeze.
But for corrosion to actually begin, there must be some defect in the lining.
One common source of defects is the significant mechanical damage associated with probing and cleaning. Solid sulfur clings so tenaciously to itself and other surfaces that hammers and chisels are needed to break it free. If the adhesion of the sulfur to the lining is stronger than the lining’s adhesion to the substrate, the lining will break away along with the sulfur, exposing bare steel. That sets the stage for corrosion beginning with the next carload.
Another example is during unloading, where in a bid to save time operators run steam through a car’s heating coils at a temperature above what is noted for proper unloading. If that temperature exceeds what the lining is rated to withstand, the lining may degrade, and corrosion could begin as soon as the car is loaded again.
Regardless of how corrosion begins, it must be stopped. The least-bad outcome of unaddressed corrosion is the premature failure of a subsequent lining. Worse than that, the continued corrosion of steel could lead to a loss of thickness sufficient to send the car back to the shop for patching. At the very worst, a tank car could become so compromised that it begins leaking molten sulfur somewhere along its journey.
Shop challenges and blending’s “backup plan”
Blending is a hard, tedious add-on to the already strenuous surface preparation process. As with any difficult manual process, there is a risk that some areas are not blended completely or are missed altogether. It also adds even more time and cost to the expensive reconditioning process. It’s not uncommon for our technical staff to inspect tank cars that badly needed blending but the process was skipped.
We never recommend skipping any form of proper surface preparation. But we also know that mistakes are made, and innovations in lining technology mean those mistakes don’t need to bite as badly.
Plasite XHT 400 is an ultra-high performance hybrid epoxy novolac seeing increased adoption in the rail and other industries where high temperatures and extremely corrosive commodities are involved. In addition to its excellent resistance to heat and harsh chemicals, Plasite XHT 400 exhibits very good flow and wetting properties. These are rare in high-solids, intricately crosslinked formulas, so the product is a great candidate for applications involving less-than-pristine surface geometries.
The image below shows the bottom nozzle of a tank car lined with Plasite XHT 400. The car was put in molten sulfur service following lining application and completed 16 load/unload cycles over a period of two years. It was then taken out of service to study its condition. Note the very good appearance of the lining despite the very uneven surface near the nozzle.
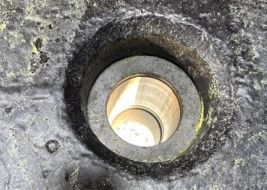
The implication for any owners, shippers, or car shops is compelling: They can, in a single coat, achieve enhanced protection of rolling stock and mitigate the risks of inadequate or incomplete blending.
Make no mistake: Blending is still necessary and will remain so. But investing in a good backup plan can eliminate some of these stakeholders’ more unwelcome surprises.